Crucial Pipe Welding Examination Tips for Quality Control
Exactly how can one guarantee the top quality of these welds that link the pipe sections? By recognizing the vital pipeline welding assessment ideas, specialists can prevent possible dangers, reduce expensive repairs, and maintain the reliability of these important infrastructures.
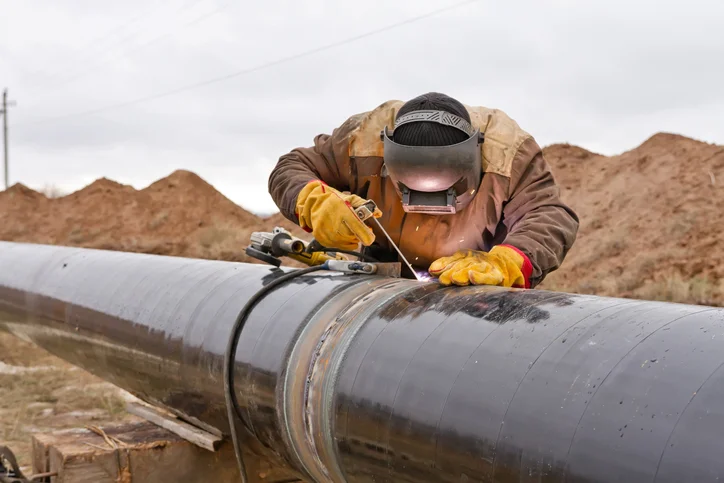
Relevance of Welding Assessment
Welding inspection plays an essential function in ensuring the architectural integrity and security of pipeline systems. By thoroughly examining welds, examiners can identify any type of flaws or flaws that can jeopardize the honesty of the pipeline. These examinations are vital for protecting against leaks, ruptures, and various other potentially disastrous failings that could lead to ecological damage, monetary losses, and also loss of life.
The value of welding examination can not be overstated, as the top quality of welds directly affects the total performance and longevity of the pipeline. Via non-destructive screening methods such as visual assessment, ultrasonic screening, radiography, and magnetic fragment testing, assessors can detect problems that might not show up to the nude eye. By identifying and dealing with these problems beforehand, welding inspection helps to make certain that pipes meet industry standards and regulative demands.
Eventually, welding assessment is a critical aspect of quality assurance in pipeline fixing, upkeep, and building (Pipeline Welding Inspection). By maintaining extensive evaluation standards, industry specialists can minimize threats and maintain the security and reliability of pipeline systems
Usual Welding Flaws
Among the difficulties encountered in pipeline welding, typical issues can considerably affect the architectural integrity and performance of the bonded joints. Splits in the weld can circulate over time, endangering the architectural integrity of the pipeline. Identifying and addressing these typical flaws via comprehensive assessment and top quality control procedures are essential for guaranteeing the integrity and safety of pipeline welds.
Evaluation Methods for Pipes

In ensuring the structural stability and dependability of pipe welds, the application of extensive assessment strategies is paramount. Various inspection methods are utilized to discover prospective flaws and make certain the total top quality of the welds. Non-destructive screening (NDT) methods such as radiographic screening, ultrasonic screening, magnetic bit testing, and liquid penetrant testing are typically utilized in pipeline welding inspection. Radiographic testing involves making use of X-rays or gamma rays to detect inner issues, while ultrasonic testing utilizes high-frequency audio waves to identify blemishes. Magnetic fragment screening works for discovering surface-breaking flaws, and liquid penetrant testing is made use of to spot surface area cracks. Visual inspection is also crucial in pipe welding to determine any noticeable issues or interruptions. Furthermore, automatic assessment methods utilizing innovative modern technologies like robotics and drones are increasingly being used to improve the efficiency and precision of pipeline inspections. By utilizing a combination of these examination techniques, pipeline bonded high quality can be assured, and possible issues can be minimized before they escalate right into larger issues.
Ensuring Quality Control Criteria
To maintain rigorous quality assurance standards in pipeline building, meticulous adherence to established market procedures and standards is critical. Quality guarantee in welding published here procedures requires a comprehensive method encompassing various stages of pipeline construction. Executing a robust quality management system that includes regular audits and reviews can further enhance the total top quality guarantee criteria in pipe welding.
Stopping Expensive Repair Work
Given the vital value of keeping rigid high quality guarantee criteria in pipe building and construction, a proactive method to stopping pricey fixings is essential. Regular maintenance checks and monitoring of environmental elements that might affect the stability of the pipe are likewise vital in protecting against pricey fixings. By spending in preventative actions and focusing on top quality guarantee at every phase of the pipe welding process, business can reduce the risk of expensive repairs and ensure the long-term reliability of their framework.
Verdict
To conclude, adherence to appropriate welding assessment methods is vital for guaranteeing the quality and honesty of pipes. By determining common welding issues and applying detailed examination procedures, costly repairs can be protected against, and quality control standards can be met - Pipeline Welding Inspection. It is important for pipeline welders to focus on evaluation procedures to keep the safety and integrity of the facilities they are working with
The relevance of welding evaluation can not be overstated, as the high quality of welds directly influences the overall efficiency and durability of the pipe. Non-destructive testing (NDT) strategies such like this as radiographic testing, ultrasonic screening, magnetic bit testing, and liquid penetrant screening are commonly made use of in pipeline welding assessment. Visual assessment is also crucial in pipeline welding to recognize any noticeable defects or interruptions. Additionally, automatic evaluation methods using advanced modern technologies like drones and robotics are increasingly being used to enhance the effectiveness and precision of pipeline assessments.In verdict, adherence to proper welding assessment techniques is necessary for ensuring about his the high quality and honesty of pipes.